客户背景
客户为河北地区一家日产5000吨的大型水泥制造企业。在熟料装车过程中,需将物料从下料口输送至卡车车斗,实现快速高效的出货。
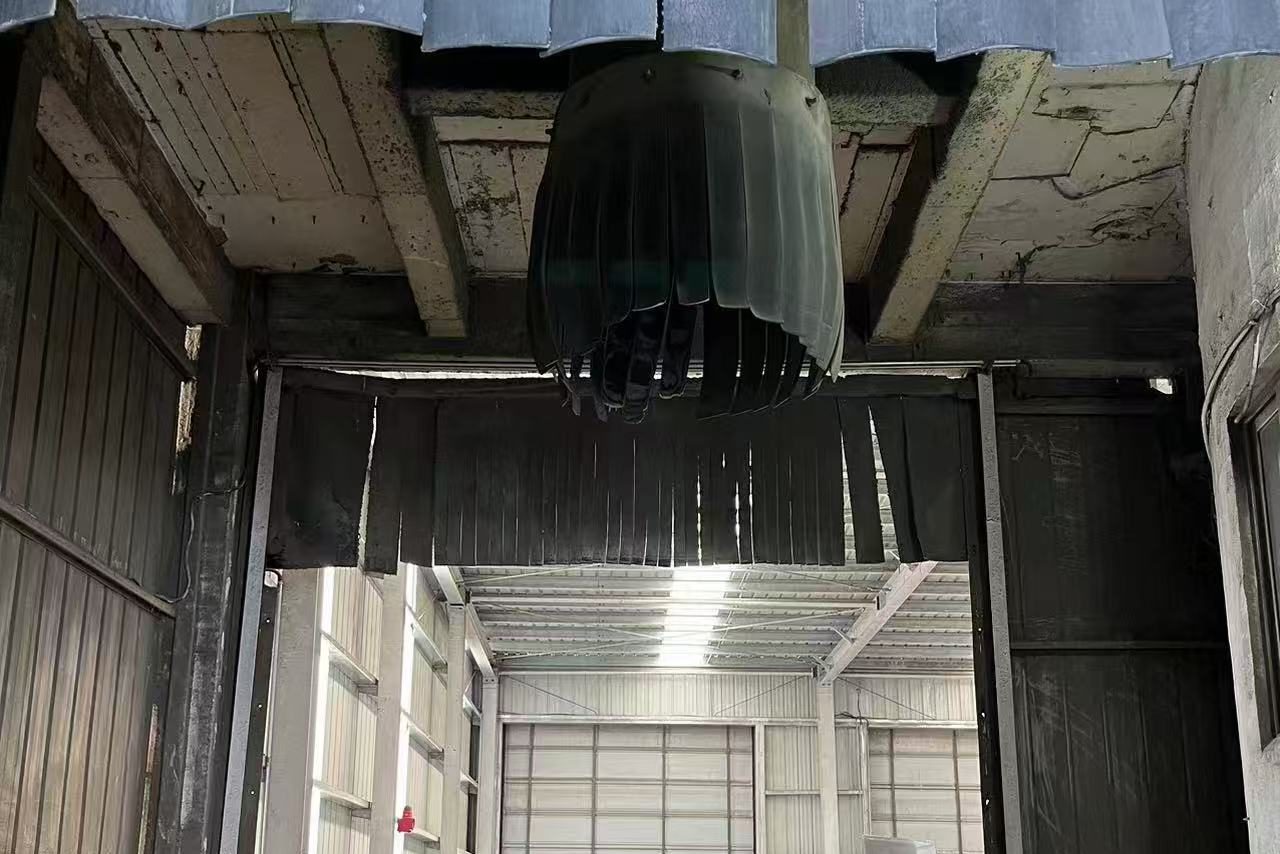
客户痛点
为增强结构强度,许多运输卡车的车厢内部设置了纵横交错的拉筋(钢筋结构)。这些结构通常分布隐蔽,且车厢高度普遍超过2米,操作人员难以直接观察其位置。
在传统人工操作模式下,操作人员依靠肉眼判断下料口的下降深度和车厢位置关系,但由于粉尘浓度高、视线严重受阻,极易导致操作失误:
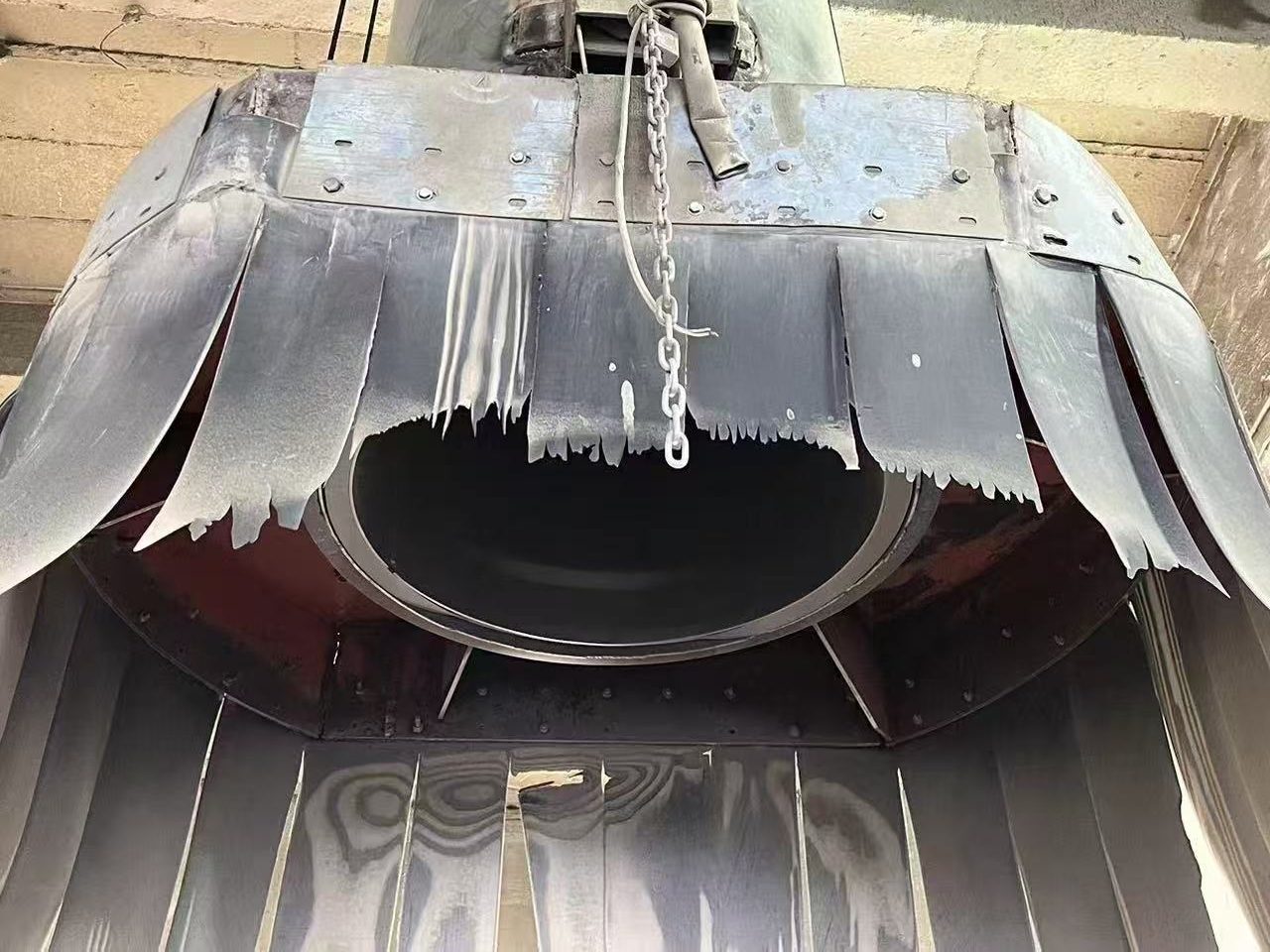
- 若下料口下降过深,可能与车厢内拉筋发生碰撞,导致设备受损;
- 若下料口未能充分接近车底,物料从高处跌落则加剧扬尘,影响作业环境和工人健康;
- 判断失误还常导致下料过多,造成熟料溢出车斗,增加清理成本和安全风险。
杉维科技解决方案
针对上述痛点,杉维科技为客户部署了自主研发的3D视觉识别系统。该系统基于激光雷达技术,具备以下关键能力:
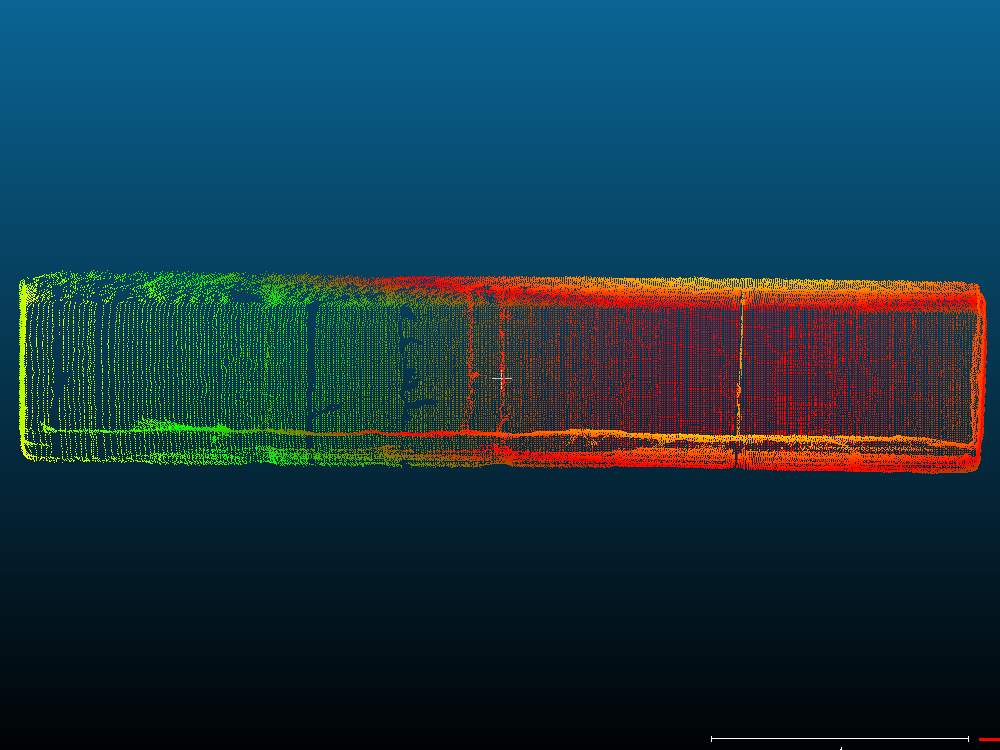
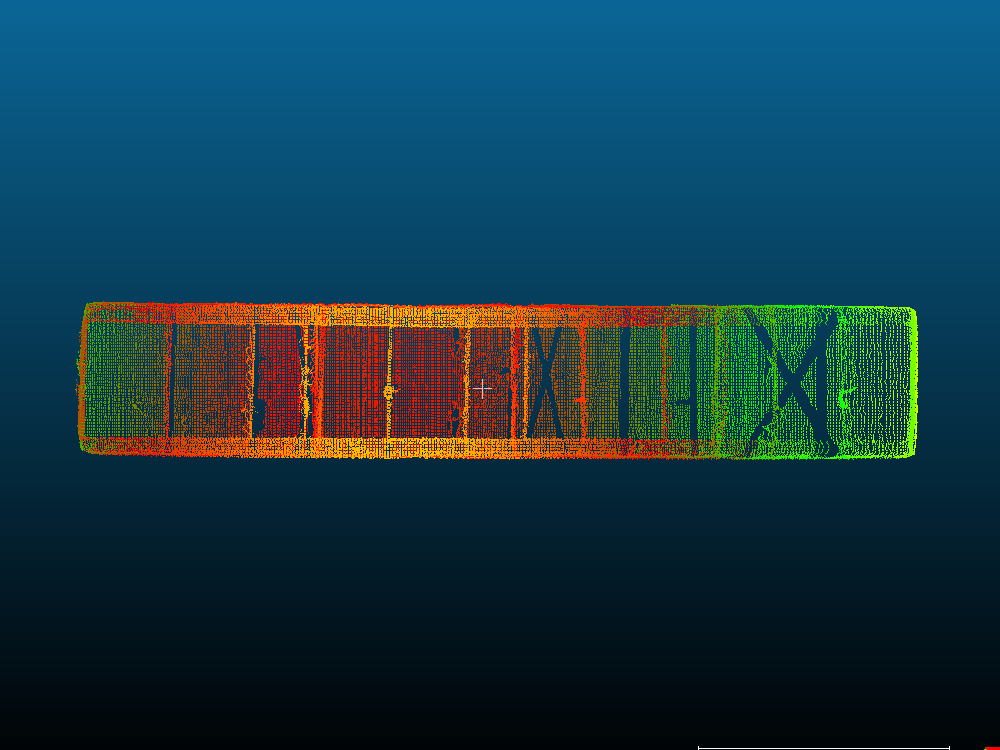
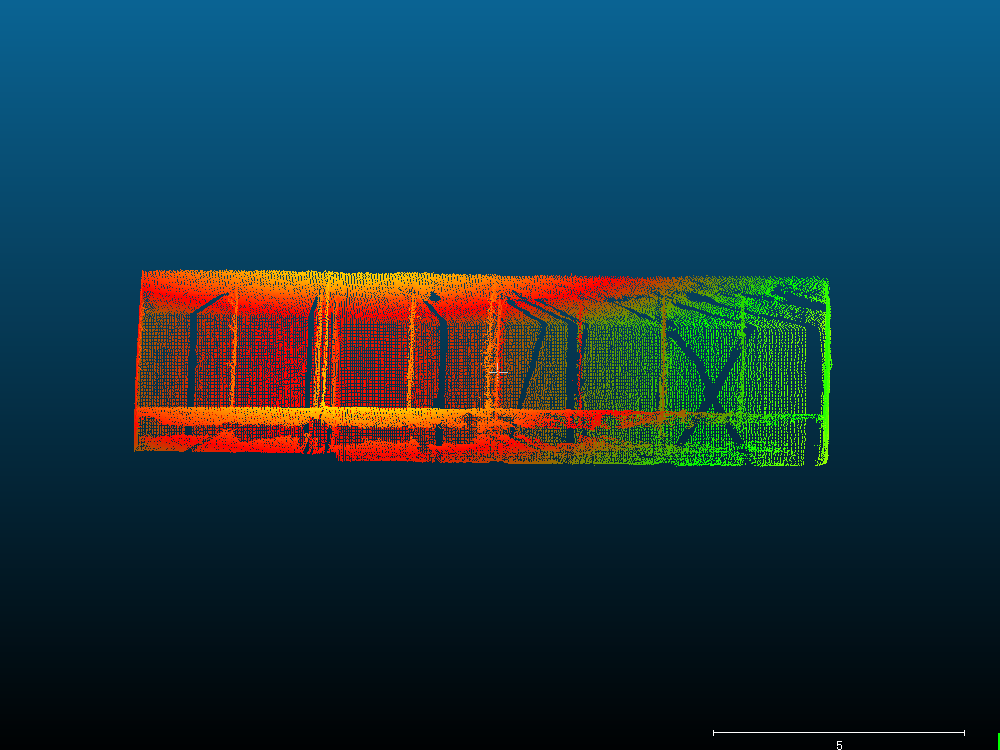
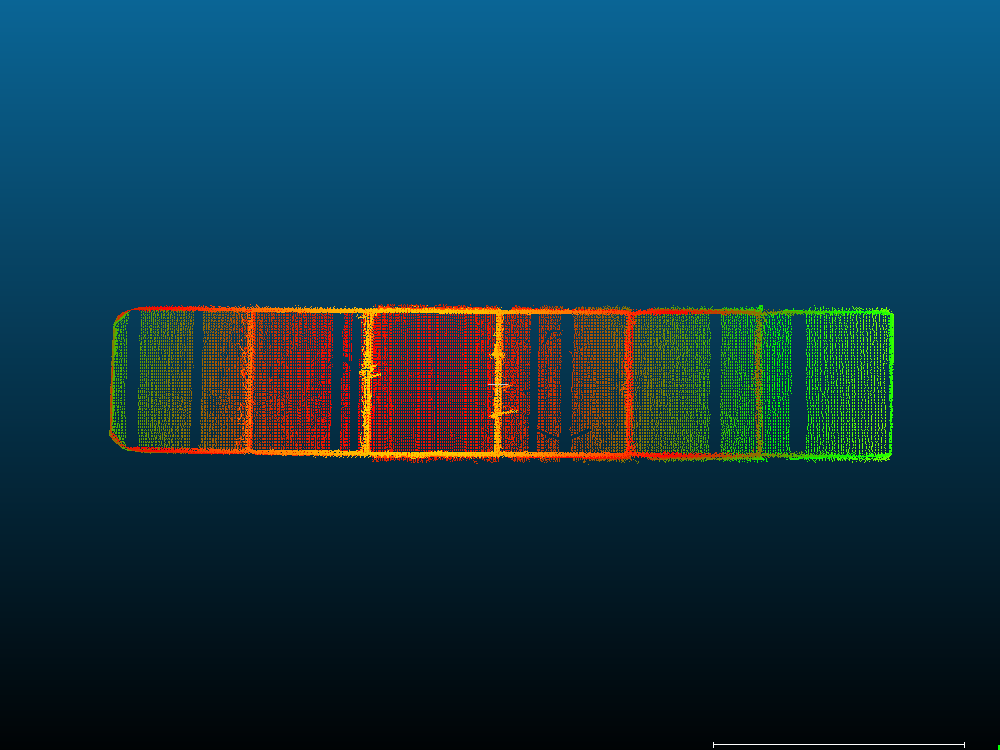
- 三维扫描建图:通过激光雷达扫描车厢内部结构,实时建立车厢的三维点云地图;
- 精准识别拉筋位置:自动识别拉筋等障碍物的空间坐标,避免碰撞风险;
- 智能联动控制:系统将障碍物坐标数据传输至PLC或上位机,实现智能化避障控制;
- 人机界面可视化:操作员可在HMI上清晰查看车厢内部结构、装料进度及安全区域;
- 安全与环保双保障:系统帮助设定合理的下料路径和深度,减少物料冲击和粉尘扩散,提升环保达标率。
客户收益
引入杉维3D视觉系统后,客户实现了从传统人工操作到智能自动装料的升级转型:
加强了生产过程的可控性与环保合规性。
有效避免了下料设备与拉筋碰撞;
显著降低粉尘排放;
提升了装车精度与效率;
减少了人工干预与安全隐患;